What motivates and drives us? Simple – helping our customers meet and master the challenges they are facing. Here at Krones, we want to develop solutions which bring about not only change but real improvements for the sector. And that only works if we focus on the precise points at which our services are used. We listen very carefully in order to understand the problems that crop up in daily production. Based on the numerous discussions we have with our customers, we develop sector-specific digital services that pull exactly the right levers for optimising a line’s performance and, in the final analysis, help reduce the total cost of ownership.
Keeping on top of complex processes, cutting costs and maximising output levels through intelligent solutions – These are exactly the kinds of tasks that Krones’ digital portfolio is aimed at. Whether it’s reducing the line operators’ workload, saving resources and energy, or visualising a production line’s most important KPIs – We offer digital services which meet all the complex requirements of the beverage and food industries.
Where do the real problems lie?
The requirements for products and processes in our industry are increasing in scope and number all the time. The reasons why production operations are getting ever more complex are many and varied: growing globalisation, changes in the sales and procurement markets, a rise in geopolitical risks, and numerous other factors. Manufacturing a highly diversified product range for a volatile market has turned into a mammoth task. How can Krones support beverage companies in coping successfully with it? By asking probing questions in regard to precisely those areas where things are not running smoothly. These include:
Many questions and factors play a vital role in the daily production routine at beverage and food manufacturers, affecting the line efficiency. But there is good news! Once the problems and the areas with scope for optimisation have been identified, the digital services offered by Krones can be put to good use there. That is because they support our customers in staying on top of the complex processes involved, in running a reliable production operation and maximising their line efficiency. So let us take a closer look at those digital services: What’s behind them? What effect do they have? How do they work and what advantages do they offer?
![]() |
Shopfloor Guidance: digital operator support in your line |
Day in, day out, the operator team face the challenge of staying on top of the various processes running in their production line. Looking after several machines simultaneously also means they cannot always be in the right place at the right moment in order to respond promptly to any problems which arise. And that is where Shopfloor Guidance comes into play. This service detects problems at an early stage, immediately notifies the relevant operators by sending a message to their smartphone, smartwatch or tablet and navigates them directly to the point where they are needed.
Moreover, the digital service gives clear recommendations on how to solve the problem in question. If a machine stops or has to be topped up with material, Shopfloor Guidance informs the operating staff immediately, stating the steps needed to eliminate or prevent the problem. If the operator cannot respond to the message, it is forwarded in line with a predefined escalation path.
And that’s not all. If necessary, the operators can additionally get context-driven support in the shape of detailed video instructions, for example, showing them step by step how to eliminate a certain problem. That means Shopfloor Guidance makes sure all the requisite measures are efficiently grouped and prioritised in order to reduce the operating staff’s daily workload with properly targeted assistance. The result? Fewer operators are needed to run the line, while its efficiency and dependability are maximised.
![]() |
Analytics: always focused on the line‘s performance |
The ability to continuously improve processes is conditional on creating transparency throughout the line. Only by keeping an eye on every piece of information on the machines and lines can opportunities for efficiency optimisation be identified and purposeful measures be derived. The challenge here is not only to record the relevant data but also to intelligently interlink and display them. The Analytics package provides just that – a comprehensive overview of the production process. Depending on their individual requirements and needs, our customers can choose from a wide range of holistically conceived and mutually compatible solutions.
Advanced Analytics provides detailed reports and insights into the causes of downtimes. Machine stops are automatically classified and KPIs (such as overall equipment effectiveness) can be calculated and displayed at the machine or line level. Advanced Analytics can be expanded to include the Integrated Analytics service which offers flexible reports at the company level and enables data to be shown in a wide range of contexts. Report templates are available, but the self-service-reporting approach also allows customers to adapt standard reports to their own individual needs and set company-specific reporting configurations. Internal benchmarking is made easy by aggregated reports on line and factory data.
The Energy and Media Reporting solution enables the consumption figures of Krones filling and packaging machines to be monitored and analysed. It helps our customers identify potential for energy savings and ways to optimise their line’s operation and thus achieve their sustainability targets. Various adaptable reports are available for evaluating the consumption figures. But it is also possible to modify the reports‘ layout and contents. This solution is continually being refined and will in future also provide an option for monitoring energy and media consumption of third-party machines.
The special focus of the Track and Trace Analytics tool is on how to solve quality problems which require a fast response. Its informative reports correlate raw materials, constituent parts and finished products, thus ensuring complete tracking and tracing and reliably identifying any suspicious products or materials. That makes it possible to have them barred from sale or recalled if necessary.
Line Diagnostics, our on-premise solution that has evolved over many years, continues to be a vital module of our digital portfolio. This comprehensive software combines the key functions needed for conducting detailed analysis of filling and packaging processes, directly detecting weak points and optimising work flows on a lasting basis.
![]() |
MSA Performance: coaching partner for optimising line efficiency |
Production data can provide valuable insights and offer genuine added value if they are interpreted correctly. Krones customers are not left to cope with all the myriads of data and figures by themselves. Our Modular Service Agreement (MSA) Performance package offers them support by Krones experts in a continuous consultation process. The experts draw up substantiated forecasts and specify suitable measures together with the client’s staff. The only precondition for benefiting from this package is use of the Advanced Analytics service on the Krones IIoT platform which provides the database for efficient coaching. Standardised reports permit the joint analysis of production runs from the past weeks in monthly consultations.
Such a consultation session starts with scrutinising all the relevant factors affecting line efficiency, but without losing sight of the overall picture. For example, unplanned downtimes are identified, and their number and duration analysed. In a second step, the malfunctions found form the basis for deriving specific fields of action.
This structured approach enables customers to obtain clarity: Is the problem in question caused by the machine, the material or by an operating error? Or are the problems rooted in the process itself? Once the cause of a malfunction has been identified, specific measures are jointly formulated and prioritised in order to get to the root of the problem. That is followed by further talks in which we assess the results obtained, thus making sure line efficiency is optimised on a lasting basis.
![]() |
Line Control: effortless coordination of orders and material |
In order to maximise a line’s efficiency and productivity, companies must make sure that everything is properly coordinated and that it all runs smoothly. And this is precisely what our digital Line Management service does: It provides central coordination of all the filling and packaging processes, starting with order-referenced specification of the production route right through to pallet labelling. The software does not see the line as a series of individual machines but as a coherent whole. So Line Management ensures a seamless flow of information, from production planning right down to each individual machine order. That means orders can be planned and processed to optimum effect.
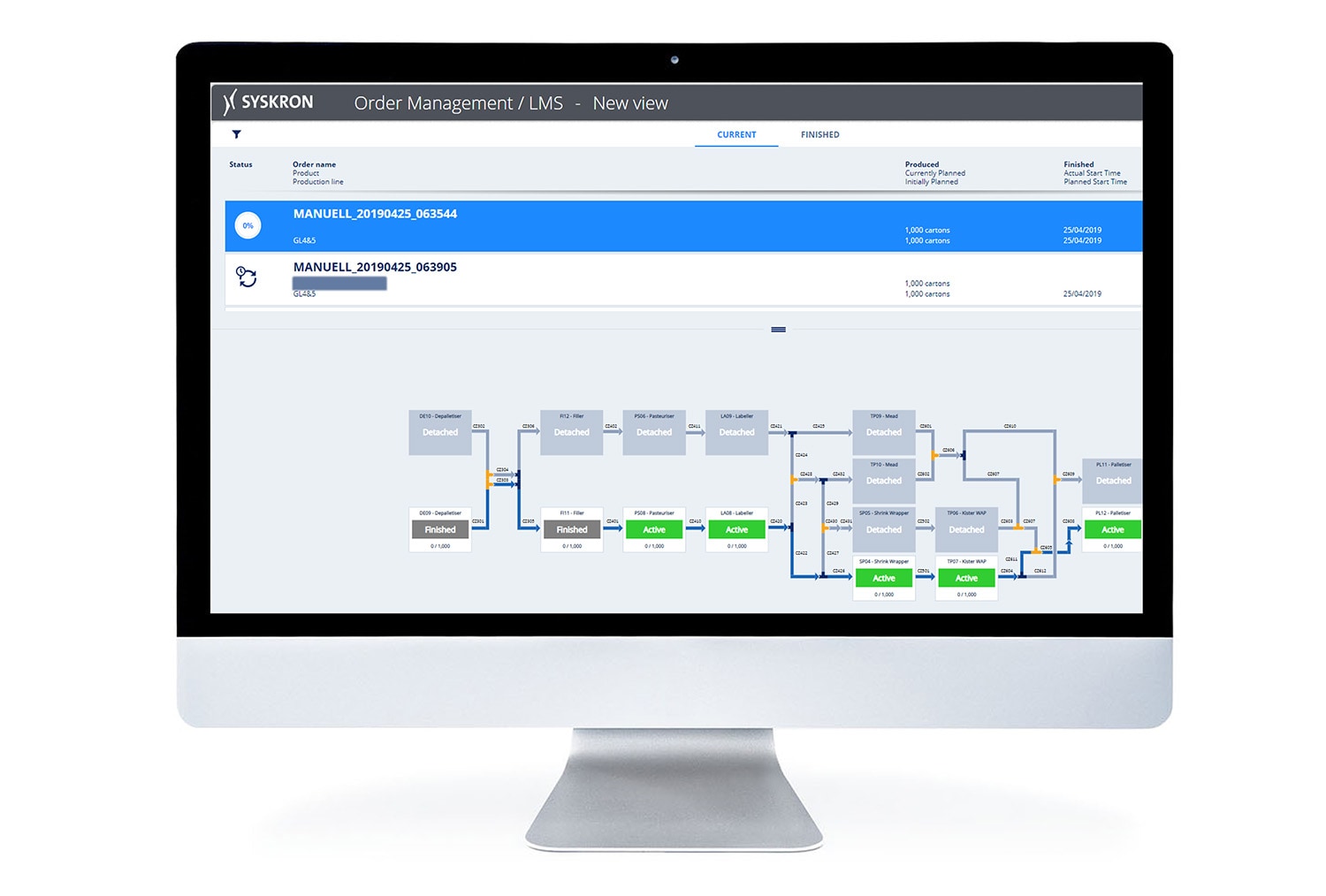
Label printers and coding units can be integrated in the line for automatic coding of important production data and sell-by dates. Line Management substantially reduces the manual work involved, effectively optimises the use of resources and raises order-processing efficiency to an entirely new level.
Another crucial factor affecting the efficiency of process sequences is how long it takes to change the line over to a different product/format. And that is where LineXpress comes into play. This software solution automates and coordinates the change-over processes in a production line by individually combining various UnitXpress quick-change modules to suit the customer’s requirements and wishes. That makes for ultra-fast product change-overs and substantially speeds up format change-overs, which likewise helps save resources.
![]() |
SAP-based solutions and SAP integration for the beverage and food industries |
Another module of our digital portfolio is based on SAP which, in combination with our broad sectoral expertise, enables us to offer efficient SAP-specific solutions which support beverage producers in making their business processes ready for the digital future. In addition to the development and engineering of SAP subscription products like Integrated Analytics, Energy and Media Reporting and Track and Trace Analytics, the SAP Beverage Template also forms part of our digital portfolio. The preconfigured template is based on SAP S/4 HANA Cloud and provides comprehensive digital representation of all the processes encountered in a factory, from planning right through to transport, thus creating the requisite transparency throughout the entire value chain.
In order to meet the increasingly varied requirements of our sector, Krones not only provides SAP-based standard solutions but also implements full-scale engineering projects in an SAP environment, covering the fields of quality management, materials management, maintenance, production planning, sales and distribution.
![]() |
Automated parameter optimisation: AI helps get the best out of your production |
Artificial intelligence is booming – not only in our private life but in industrial applications as well. And for good reason because its potential is enormous. Krones has developed an intelligent system for the Contiform stretch blow-moulder in the shape of Contiloop AI. This innovative solution combines AI-based software with newly developed hardware in order to detect even the smallest of deviations in material distribution during PET-container production, and to automatically modify the relevant stretch blow-moulding parameters in real time. This results in consistently high bottle quality. Thanks to automated trial runs and integration of a control algorithm known as AI agent, the stretch blow-moulding process is precisely regulated and continuously optimised under changing conditions. That means Contiloop AI not only relieves the operators’ workload, it also contributes to sustainability by making sparing use of resources since it reduces the consumption of PET and CO2.
Contiloop AI, however, is not the only digital solution developed by Krones that uses artificial intelligence. Our Linatronic AI empty-bottle inspector is also based on deep-learning technology and transforms the checking of empty containers. Instead of conventional image processing algorithms, it uses neuronal networks which are trained with a multiplicity of images. That enables the machine to distinguish more precisely between defective and flawless units, thus substantially reducing the number of erroneously rejected bottles. Not only does this improve overall quality levels, it also helps achieve significant savings in the use of resources.
Holistic and innovative – for a better world
It’s not only our customers who benefit from our comprehensive digital portfolio, which is designed to increase line performance and cut operating costs. We’re transforming the entire sector bit by bit, by using our services to eliminate all manner of production weak points, large and small. Creating a more efficient, more sustainable industry is our contribution towards a better world, something that ultimately benefits every one of us.